Driving Toward Driverless
We hear quite a bit in the popular media about driverless vehicles – Tesla’s futuristic driverless lorries, Google’s driverless cars. But less media attention is spent on driverless agricultural implements, despite some very innovative progress in that area.
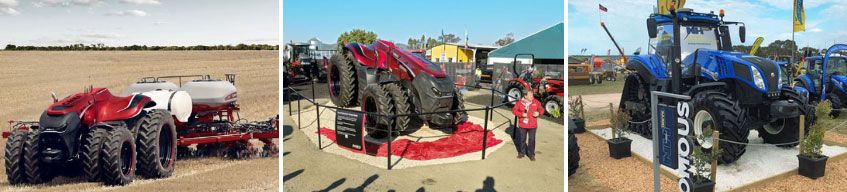
Case and New Holland’s Driverless Tractors
The Push for Driverless Ag Tech
Getting to driverless vehicles is a challenge for designers, engineers, and manufacturers. Regardless of the type of vehicle or the developer, the successful operation of all driverless technology hinges upon a complex combination of sensors, cameras, and scanners, and the potential for issues with this technology is significant. Even though driverless cars and lorries operate in the less harsh and somewhat more controlled conditions of city streets, both cars and driverless tractors are influenced by environmental factors like heavy dust and adverse weather. Add these environmental impacts to the developmental challenges of technology, safety, and regulation, and you can begin to understand the long road ahead for driverless tech.
This long road hasn’t deterred manufacturers from chasing the dream of driverless tractors, however. Major international manufacturers like John Deere, Case New Holland (CNH) and AGCO Fendt are all actively developing solutions, as are a few small ag tech start-ups. Each company is approaching the driverless challenge from a unique angle, modifying their vision as technologies change or innovations create new opportunities.
Technological approaches vary by manufacturer and reflect industry trends or producer needs. The three main approaches are relationally-guided autonomy, swarm technology and self-guided autonomy, and we’ll look at some innovations in each type.
Relationally-Guided Autonomy
AGCO Fendt started the relationally-guided autonomy style of driverless tech with its GuideConnect product, originally developed in the 2000s. This tech was an upgrade of autosteering technology, and based itself off of two tractors operating in proximity to each other within paddock utilizing a single operator. The single operator ran one tractor, called the pilot tractor. The second tractor functioned driverlessly, taking its cues for turning at headlands and maintaining row spacings from its position in relationship to the operator-driven pilot tractor, hence the “relationally-guided” name.
Despite being called a driverless technology, this approach still required a driver/operator. Getting away from an onboard operator was a key goal of driverless, so this type of driverless technology has largely been abandoned.
Self-Guided Autonomy
The path to self-guided autonomy is one chosen by major manufacturers John Deere and CNH. John Deere has had autosteer technology based upon GPS location and other embedded tech for years, allowing tractors and harvesters to operate in perfectly straight lines, but current autonomous offerings require an onboard operator. Deere engineers are working through the roadblocks to full autonomy[1], but haven’t yet released a prototype for public viewing.
Deere competitor CNH is a step ahead on autonomy from this perspective, making waves in the US[2] and Australia[3] in the past two years with their futuristic-looking, cab-less, driverless, self-guided tractor. While no production timeline is public or guaranteed, the tractor has been making the rounds at farm shows and expositions, giving the farmers a look at the future of their operations.
Swarm Technology
The rise of drones has contributed to the development of swarm technology as a “driverless” approach to production farming. Rather than relying on large, standalone tractors and harvesters, swarm tech is designed to utilize smaller pieces of equipment governed by a large central “brain.”
AGCO has developed swarm technology for sowing operations in the Fendt Xaver autonomous swarm model[4]. The autonomous Fendt sowing units are small, and dozens of them are transported by a logistics unit, which is capable of being pulled by a standard pickup truck. This logistics unit also helps direct the operations of the swarm units, functioning as a “brain” which the sowing units access to receive information for and feedback on their work.
Independent researchers and drone operators are also utilizing this approach. The Hands Free Hectare, a barley production project headed by researchers in the UK, recently completed the world’s first hands-free harvest by implementing a swarm-based solution overseen by drones[5].
Start-ups Bridge the Gap
American startup company Autonomous Tractor Corporation is also working in the autonomous space, but in a way unlike its big-name competitors. Rather than trying to design standalone equipment, the company is focusing on overcoming the challenges of autonomy. ATC’s focus has resulted in more easily managed sensor arrays and artificial intelligence-driven navigation systems. These allow autonomous tractors to “learn” the paddocks they cover. This makes them more intelligent and efficient with each season. Once ATC’s programs fix these autonomy challenges, they’re hoping to partner with manufacturers to integrate their solutions into new generations of equipment.
A true driverless tractor is still years away, but as in many facets of life, technology and innovation keep pushing us closer to an autonomous reality.